CCHI thermal engineering expert team & our partners has developed several types of heat exchanger
with our own patent technology in designing dimple plate H.E., coil-wounded pipe H.E., and twisted-tube
H.E. which has a significant increase of heat exchange efficiency comparing to traditional heat exchangers, decrease
fabrication cost and dramatically decrease operation cost of the heat exchangers.
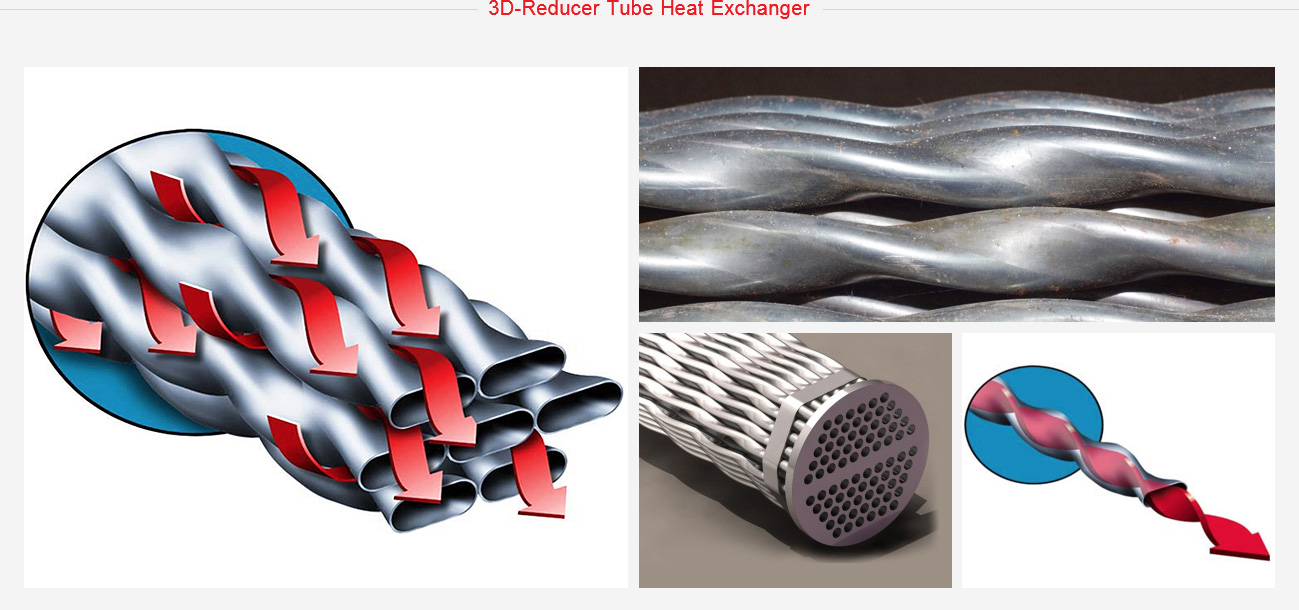
3-D reducer tube heat exchanger, by applying contract flow heat exchange feature, fluid volume match fluid speed, increase heat exchanger efficiency, decrease shell side pressure drop,reaches different effect for different operation environment.
SP type heat exchanger can increase heat exchanging efficiency by 20~30%, decrease volume by 20%, and safe material for 15%~30%
In refrigeration system, this type of heat exchanger has a 20% smaller volume and 30% lower weight.
Applicable in power plant, metallurgy, pulp mill, printing, glass and rubber, food and pharmaceutical and petro-chemical plant. Can be used to replace or upgrade traditional type of heat-exchanger
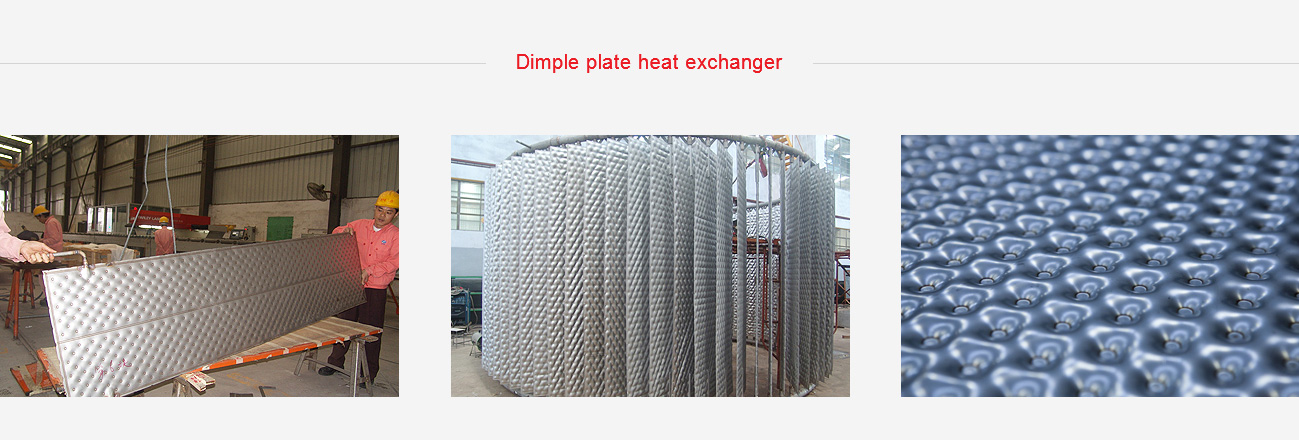
CCHI applies laser welding technology and our patent manufacturing technology in dimple plate Heat Exchanger. It helps to create more vortex of the fluid in the dimple plate and increase the heat exchanging area.
According to data from our client, dimple plate heat exchanger increase 50%~80% of the heat exchanging efficiency of the H.E., and reducing 30%~50% of cost during operation comparing to tradition shell and tube H.E. It is applicable in clean internal fluid and low pressure environment.
Multi-convection heat exchanger with the special features of the geometry and the possibility to use various materials allow a wide range of applications. It is manufactured in stainless steel, aluminium alloy, carbon steel and special alloys.
Heating surfaces of up to 40,000 square meters and more can be installed in oneunit. Bundle diameters of approx. 5,500 mm and unit weights up to 250 metric ton.
Benefit:
•Broad temperature and pressure ranges
•Multiple fluids can be treated in one exchanger
•Compact unit with large specific heat transfer area per volume
•Robust design suitable to cope with transient off-spec conditions
•Integrated two-phase separator and distributor, if required
•No bundle sagging due to proprietary support system
•100% self-draining
•Available in various materials
Possibility for bundle temperature recording